June 30, 2025
Sustainable and Circular Design: Repurposing Single-Use Plastics
By transforming discarded single-use plastics into second life refrigeration parts, we’re reducing costs and scaling decarbonization, creating a circularity blueprint for our global supply chain.
Circularity isn’t a side project at Trane Technologies - it’s embedded in every product decision we make. By designing for disassembly, choosing materials that can be reused or remanufactured and prioritizing recycled materials, we extend product life, cut waste and find potential opportunities to lower costs.
Sustainable and circular design is a cornerstone of this approach. When our product engineers start developing new products, they plan for every stage of the equipment’s lifecycle.
They integrate design methodologies to ensure products have the highest potential recycled content, and are able to be remanufactured, repurposed or reclaimed instead of discarded at end of life. This lifecycle thinking propels us toward our 2030 Sustainability Commitments, including our targets to send zero waste to landfill, achieve a 40 percent reduction in embodied carbon in our products, and our Gigaton Challenge to help our customers decrease their greenhouse gas emissions by one billion metric tons.
These circularity practices provide a blueprint for supply chain decarbonization and business growth. The journey of a small plastic zip tie - reborn as a critical refrigeration part - shows just how powerful that blueprint can be.
Innovative solutions for single-use plastics
Our Barcelona facility that makes Thermo King products receives over 400,000 zip ties each year on parts and components from suppliers. The ties are made from strong, durable plastic known for its resistance to wear, making them a valuable and underutilized resource. How could this material be leveraged instead of discarded?
The facility’s Green Team - Ricard Canela, Rubén Fernández and Marina Invernón - decided to find a way to reuse the zip ties in a new design for high-value components, repurposing them into new drain tubes for the units they manufacture. The team invested in an on-site shredding unit for the discarded zip ties. After shredding, the plastic is sent to a partner. There, it is melted and shaped into closed-loop drain tubes for Thermo King refrigeration units.
Circularity keeps products, equipment and infrastructure in use for longer, improving resource productivity.
Rubén Fernández
Truck Engineering Lead, Thermo King EMEA
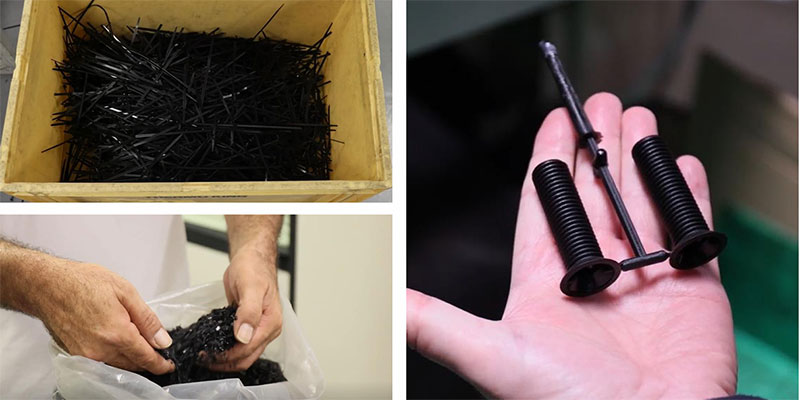
Plastic zip ties collected and recycled into drain tubes for Thermo King units.
In the first year, this circular design strategy repurposed 450,000 zip ties into 50,000 drain tubes, enough to support the demand within 27,000 refrigeration units. The project cut carbon emissions by 4.3 metric tons. This is like removing the carbon footprint of 4,778 pounds of coal burned or equal to driving a gasoline car for 10,953 miles.
The team also designed the operational process so that other manufacturing locations can replicate it. With a small investment, production sites around the world can change their single-use plastics into valuable parts. This helps reduce carbon emissions and saves waste across our global organization.
Circularity reduces our carbon footprint
This effort is not just about a new way to make a refrigeration part. It’s about embedding circularity into how our teams think and work, helping us define the value and lifecycle thinking in business. The initiative shows that sustainable business practices don’t have to start with big changes. They can begin with something simple, like a zip tie, to inspire other smart and creative design changes.
As rules for single-use plastics and emissions become stricter, closed-loop methods help future-proof our portfolio. They also allow our teams see “waste” in a new way which helps advance our goal of zero waste to landfill. Collectively, these efforts inspire the next steps in our decarbonization strategy, moving us forward as a sustainable business and enhancing our value chain.
Explore more about how embracing circularity can drive business value in our series on this topic.
Topic Tags