As a climate innovator, we are changing how the world uses heating and cooling technology and solutions on a global scale. Propelled by our purpose to boldly challenge what's possible for a sustainable world, we are leading our industry and setting the standard for growth through sustainability. Our 2024 Sustainability Report details the actions that have put us on track to meet our ambitious sustainability commitments and deliver value for our customers. It outlines how we embed sustainability into our business model. And, it’s a story about our people taking action to have an uplifting impact on the environment, society and our business.
2024 Sustainability Highlights
237M
metric tons of CO2e reduced from our customers’ carbon footprint since 2019 as part of our Gigaton Challenge
82
overall employee engagement score (out of 100), reflecting top quartile among benchmarks in 2024
44%
reduction in operational emissions since 2019, progressing toward our science-based target of 50% by 2030
Five years of building momentum
Chair and CEO Letter to Stakeholders
Our ability to deliver leading financial performance while advancing our bold sustainability commitments demonstrates there is no trade-off. For Trane Technologies, sustainability is at the center of our strategy and drives strong financial results over time.
I am immensely proud of our team and what we have accomplished together. The year 2025 marks our fifth anniversary as Trane Technologies. We are five years older, and five years bolder, and I am confident our brightest days are ahead.
Committed to transparency
Recognition
We are proud to highlight recognition and ratings we’ve received for our industry-leading business and sustainability performance from some of the world’s top organizations.
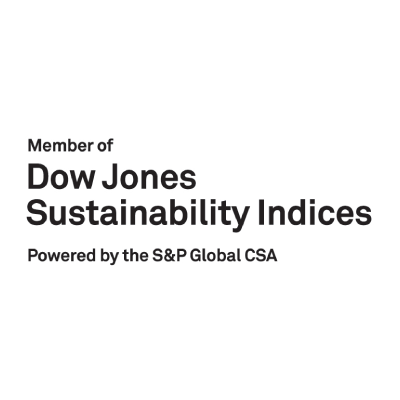
Dow Jones Sustainability Index
- 14th consecutive year on North America Index, 4th on World Index
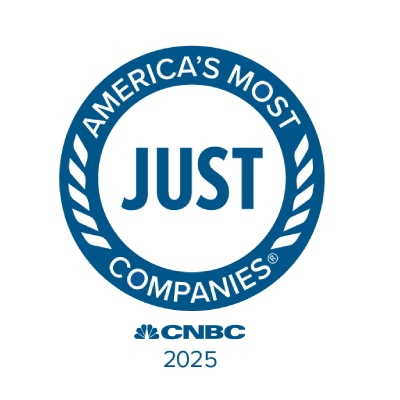
JUST 100
- Ranked 6th overall, 1st in the Building Materials & Construction Industry
- 4th consecutive year on the list
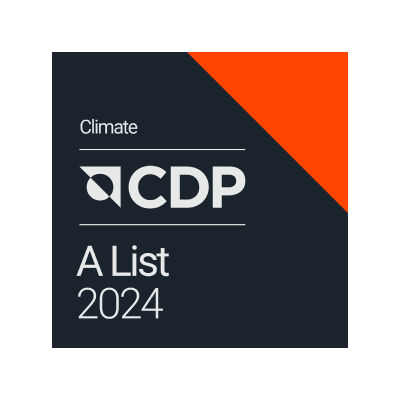
CDP
- Climate score: A, for 3rd consecutive year
- Water score: B-, 5th consecutive year listed
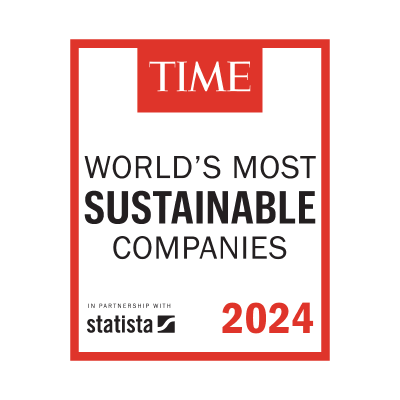
TIME
- World’s Most Sustainable Companies, ranked 65th overall
- World’s Best Companies for Sustainable Growth
- World’s Best Companies
Previous Reports
Some information on these pages may relate to historical data for Trane Technologies plc (formerly known as Ingersoll-Rand plc) as a combined company operating with two business segments: Climate and Industrial. In the first quarter 2020, we completed a spin-off of our Industrial business which was subsequently combined with Gardner Denver Holdings, Inc. (“GDI”). GDI was subsequently renamed Ingersoll-Rand, Inc.